Horizon Power
Industry
Power transmission and distribution
Devices
Ground-based cameras and tasked satellites
A.I. Apps
PowerlineAI and IlluminatorAI
Deploying on-ground and space-based vision to modernize asset inspections
Background
Inspections are necessary to ensure that power lines are well-maintained, are in a safe state, and meet regulatory requirements.
Current data collection over often rugged, remote terrain is cumbersome, time-consuming, and costly. The modus operandi, using a ‘spotter’ in a helicopter, is expensive, has limited access in narrow air ‘corridors’, and consolidating the ‘subjective’ data for an area the size of Alaska and California combined, is subject to a slow turnaround time.
Inspecting power lines at ground level is similarly time-consuming and costly: it is a dangerous job as workers can be electrocuted if their equipment connects with a cable while touching the ground.
Computer vision is a paradigm shift: reducing risk, speeding up inspections and reporting, and delivering objective analysis, as well as providing a time-based comparison of the cables, towers, poles, and street lights. All of these make it possible to improve service delivery to customers, improve safety, and comply with regulations cost-effectively.
Horizon Power expressed interest in gaining, and maintaining, a deeper understanding of the working status of their distributed assets. They engaged Unleash live to conduct two separate projects to evaluate the effectiveness of remote asset inspections and to test the use of A.I. for inspecting and maintaining their distributed assets.
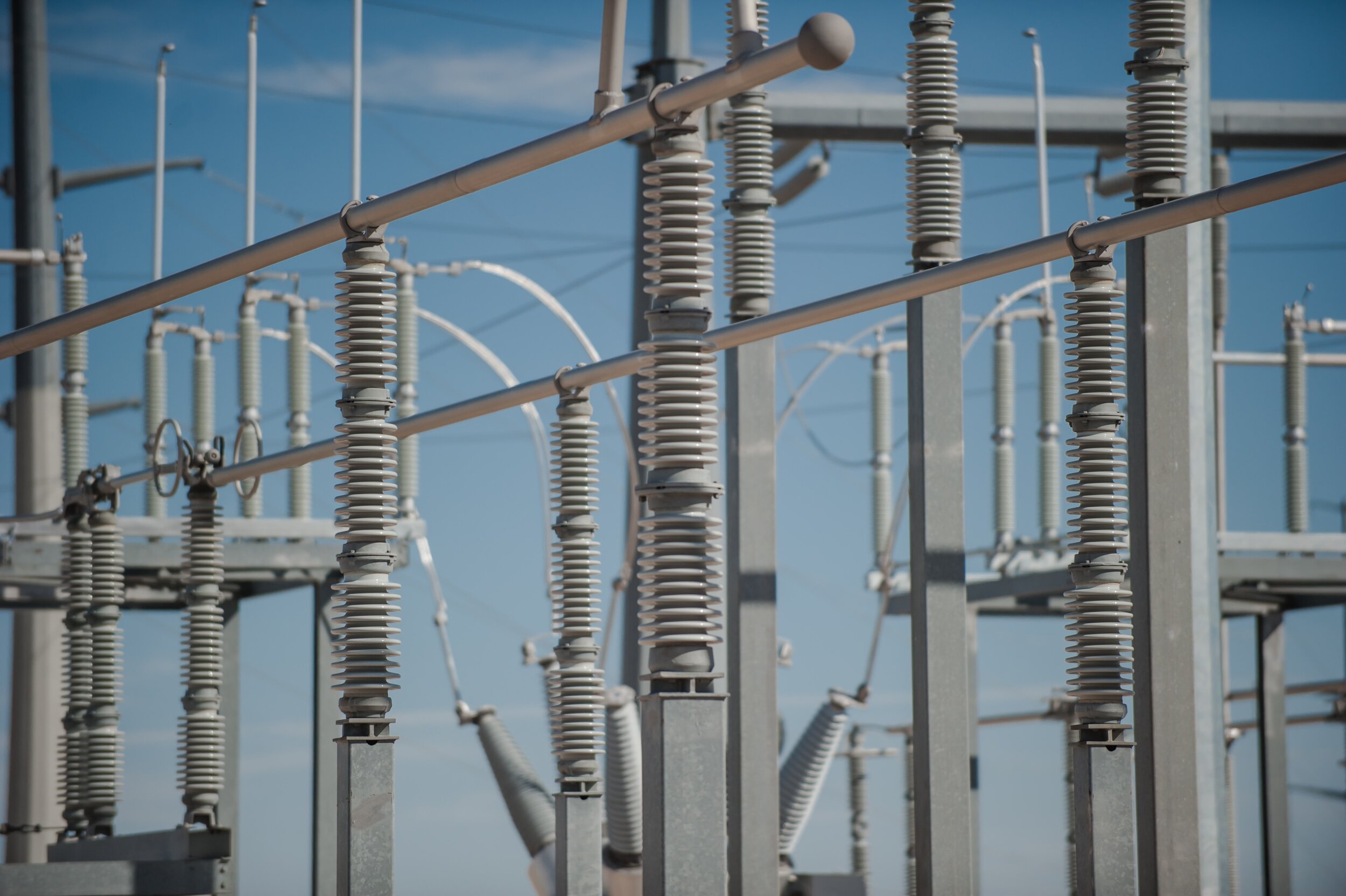
Challenge
Horizon Power supplies electricity to over 100,000 residents and 10,000 businesses across regional Western Australia, an area of 2.3 million square kilometers (or one customer per 50 square kilometers).
The existing primary inspection processes relied heavily on manual data entry, subject matter experts, and report writing. This makes it difficult to efficiently scale inspections across their dispersed customer base.
Given the number of their power assets and the size of their area of responsibility, dispatching regular ground-based patrols to conduct condition monitoring assessments is extremely time-consuming and expensive. An inspection team would typically take 2 days to travel and inspect illuminators in a remote town, where there may well be no fault.
To improve on this approach, the Horizon Power digitization team evaluated the available ‘best in class’ technologies to develop informed, data-driven, decision-making operations and approached Unleash live to deliver a solution.
How it was done
Unleash live applied the following approaches:
Using our Powerline Inventory A.I. app, coupled with A.I. thresholding, we detected the components on the power distribution grid, and automatically generated reports on their operational status, identifying whether they are undamaged, rusty, or damaged. Using ground-based cameras, a crew collected 53,000 images and these were run through our A.I. app to validate its accuracy when compared to existing inspection results.
Using tasked satellites to collect high-resolution imagery over specific areas at night, our custom A.I. app determined the illumination levels for selected areas. This data was cross-referenced to a digital asset map, to confirm the asset’s continuing operation and to identify any malfunction.
A visual analytics solution for energy providers and flight operators
“This particular piece of work has gone a long way to help us understand and confirm how these types of technologies can significantly benefit our inspection, maintenance and operational activities going forward”
Ray Achemedei
GM Technology & Digital Transformation
Reduce turnaround time from months to hours
53,000 images were collected and analysed by Unleash live in hours
Real-time insights lead to action
Unleash live delivered objective insights in real-time for both projects directly to Horizon Power through a variety of formats, including CSVs, PDFs, and APIs, to ensure compatibility with the existing internal reporting infrastructure.
Inspections can now be done with satellites and Unleash live’s A.I., the results of which can then be cross-referenced with ground-based inputs to reduce any false positives.
By using Unleash live’s A.I. to process images real-time in the cloud, multiple parallel streams concurrently processed the 53,000 images and reduced the turnaround time from months to hours.
With ready access to the insights across the organization, personnel on the ground can access experts and executives in video conferences to explore and prioritize repairs, and troubleshoot any less urgent matters.